How Much Does It Really Cost to Build a Loading Dock?
Building a loading dock is a crucial investment for businesses that rely on the efficient movement of goods. Whether you’re a warehouse manager, a logistics coordinator, or a business owner aiming to streamline your operations, understanding the costs associated with constructing a loading dock is essential. From the initial design to the final construction, various factors can influence the overall expense, making it vital to approach this project with a clear understanding of what to expect. In this article, we’ll delve into the financial considerations and key elements that contribute to the cost of building a loading dock, ensuring you’re well-equipped to make informed decisions.
When contemplating the construction of a loading dock, several variables come into play that can significantly affect the overall price. These include the size and design of the dock, the materials used, and the specific features required for your operation. Additionally, location plays a pivotal role; urban areas may present higher labor costs and zoning regulations that could impact your budget. Understanding these factors will help you gauge what kind of investment you’re looking at and how to plan accordingly.
Moreover, it’s essential to consider the long-term benefits of a well-constructed loading dock. While the initial costs may seem daunting, an efficient loading dock can enhance productivity, reduce operational delays, and improve safety for your workforce.
Factors Affecting Loading Dock Construction Costs
The cost of building a loading dock can vary significantly based on several factors. Understanding these elements can help businesses plan their budgets more accurately. Key factors include:
- Location: The geographical area affects labor costs, material availability, and local regulations.
- Dock Size and Configuration: The dimensions and design of the loading dock (e.g., straight, angled, or recessed) play a crucial role in determining overall costs.
- Materials Used: The choice between concrete, steel, or composite materials will influence the expense. Higher-grade materials often result in increased durability but at a higher initial cost.
- Equipment Needs: Additional equipment like dock levelers, bumpers, and safety features can add to the total expenditure.
- Labor Costs: Variability in labor costs based on local wage rates and availability of skilled labor can impact the final bill.
Estimated Costs for Loading Dock Construction
The average cost to build a loading dock typically ranges from $10,000 to $100,000 or more, depending on the factors mentioned above. Below is a breakdown of potential costs associated with different elements of loading dock construction:
Component | Estimated Cost Range |
---|---|
Basic Construction | $10,000 – $50,000 |
Dock Levelers | $1,500 – $5,000 each |
Safety Equipment (Bumpers, Lights) | $500 – $3,000 |
Drainage Systems | $1,000 – $5,000 |
Permits and Inspections | $500 – $3,000 |
Additional costs may arise from customization, such as installing specialized loading equipment for unique freight needs.
Maintenance and Operational Costs
Beyond initial construction, loading docks incur ongoing maintenance and operational costs that should be factored into the overall budget. These include:
- Routine Maintenance: Regular inspections and repairs can cost anywhere from $500 to $2,000 annually.
- Equipment Replacement: Dock levelers and safety equipment may require replacement every 5-10 years, costing several thousand dollars.
- Utilities: Additional energy costs for lighting and heating can add up, particularly in colder climates.
By planning for these expenses, businesses can ensure the longevity and functionality of their loading docks while maintaining operational efficiency.
Factors Influencing Loading Dock Construction Costs
The cost to build a loading dock is influenced by several key factors that can significantly affect the overall budget. These include:
- Location: Costs can vary greatly depending on the geographic area and local market conditions. Urban areas may have higher labor and material costs compared to rural locations.
- Design Complexity: A simple, standard design will typically be less expensive than a customized dock that requires unique features or architectural elements.
- Materials Used: The choice of materials, such as concrete, steel, or specialized coatings for durability, can impact costs.
- Dock Levelers and Equipment: Additional features such as hydraulic or mechanical dock levelers, safety barriers, and lighting will increase the overall expense.
- Site Preparation: Costs associated with grading, paving, and drainage systems can add to the total, particularly if the site requires extensive preparation.
- Labor Costs: The availability and cost of skilled labor in the region can affect the overall project budget.
- Permitting and Regulations: Compliance with local building codes and zoning regulations may incur additional fees and time delays.
Estimated Cost Breakdown
The estimated costs associated with building a loading dock can be categorized into several components. Below is a general breakdown:
Component | Estimated Cost Range |
---|---|
Site Preparation | $5,000 – $15,000 |
Concrete Paving | $10,000 – $25,000 |
Dock Equipment (Levelers) | $2,000 – $10,000 each |
Structural Frame | $15,000 – $30,000 |
Safety Features (Barriers) | $1,000 – $5,000 |
Electrical and Lighting | $1,500 – $5,000 |
Permitting and Fees | $1,000 – $5,000 |
Total Estimated Cost | $36,500 – $95,000 |
Cost Variations by Dock Type
Different types of loading docks come with varying costs due to their design and functionality. Common types include:
- Standard Loading Dock:
- Cost: $30,000 – $50,000
- Features: Basic design, typically used for general warehousing.
- Recessed Loading Dock:
- Cost: $40,000 – $70,000
- Features: Built into the building structure, allowing for easier access.
- Elevated Loading Dock:
- Cost: $50,000 – $90,000
- Features: Raised to accommodate specific vehicle heights, often used in multi-story facilities.
- Mobile Loading Dock:
- Cost: $20,000 – $40,000
- Features: Portable and flexible, suitable for varying locations.
Additional Considerations
When planning for a loading dock construction, consider the following additional expenses that may arise:
- Maintenance Costs: Regular maintenance and repairs can add to long-term expenses.
- Insurance: Adequate insurance coverage for the loading dock and associated operations is necessary.
- Future Expansion: Plan for potential future needs and expansion, which may require additional investment.
Understanding these factors and cost breakdowns will help in budgeting and making informed decisions regarding loading dock construction. Proper planning and consideration of all elements can lead to a successful project outcome.
Cost Considerations for Building a Loading Dock
Mark Thompson (Construction Project Manager, Dock Solutions Inc.). “The cost to build a loading dock can vary significantly based on factors such as location, materials, and design specifications. On average, businesses can expect to spend between $30,000 to $100,000 for a standard loading dock installation.”
Lisa Chen (Logistics Analyst, Freight Forwarding Experts). “In addition to the initial construction costs, companies should also consider ongoing expenses such as maintenance and repair. A well-built loading dock can lead to reduced operational costs in the long run, making it a worthwhile investment.”
James Patel (Industrial Engineer, Supply Chain Innovations). “When budgeting for a loading dock, it is crucial to include additional features like safety barriers, lighting, and drainage systems. These enhancements can increase the total cost but are essential for ensuring a safe and efficient loading environment.”
Frequently Asked Questions (FAQs)
How much does it cost to build a loading dock?
The cost to build a loading dock typically ranges from $10,000 to $50,000, depending on factors such as size, materials, and location. Custom features may increase this estimate.
What factors influence the cost of constructing a loading dock?
Key factors include the type of loading dock (e.g., ground-level vs. elevated), materials used, site preparation requirements, local labor costs, and any necessary permits or inspections.
Are there ongoing maintenance costs for a loading dock?
Yes, ongoing maintenance costs can include repairs, resurfacing, safety inspections, and equipment upkeep. Budgeting for these expenses is essential for long-term functionality.
What permits are required for building a loading dock?
Permits vary by location but typically include building permits, zoning approvals, and possibly environmental assessments. It’s crucial to check with local authorities for specific requirements.
Can I build a loading dock myself to save costs?
While DIY construction may reduce labor costs, building a loading dock requires specialized knowledge and compliance with safety regulations. Hiring professionals is often recommended to ensure quality and safety.
What are the benefits of investing in a loading dock?
Investing in a loading dock enhances operational efficiency, improves safety for loading and unloading, and can increase property value. It also facilitates better logistics and inventory management.
In summary, the cost to build a loading dock can vary significantly based on several factors, including the size and design of the dock, the materials used, and the specific location. On average, businesses can expect to invest anywhere from $10,000 to $50,000 for a basic loading dock installation. However, more complex designs or additional features such as hydraulic lifts, canopies, or specialized flooring may increase this cost substantially.
Furthermore, it is essential to consider ongoing expenses associated with the maintenance and operation of a loading dock. These can include routine repairs, safety equipment, and staff training to ensure compliance with safety regulations. Planning for these additional costs is crucial for businesses to maintain efficient operations and avoid unexpected financial burdens.
Ultimately, when budgeting for a loading dock, it is advisable to conduct thorough research and obtain multiple quotes from contractors. This will provide a clearer understanding of the costs involved and help in making informed decisions that align with the specific needs of the business. Investing in a well-designed loading dock can enhance operational efficiency and contribute to the overall success of logistics and distribution efforts.
Author Profile
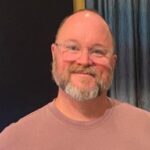
-
I’m Leonard a developer by trade, a problem solver by nature, and the person behind every line and post on Freak Learn.
I didn’t start out in tech with a clear path. Like many self taught developers, I pieced together my skills from late-night sessions, half documented errors, and an internet full of conflicting advice. What stuck with me wasn’t just the code it was how hard it was to find clear, grounded explanations for everyday problems. That’s the gap I set out to close.
Freak Learn is where I unpack the kind of problems most of us Google at 2 a.m. not just the “how,” but the “why.” Whether it's container errors, OS quirks, broken queries, or code that makes no sense until it suddenly does I try to explain it like a real person would, without the jargon or ego.
Latest entries
- May 11, 2025Stack Overflow QueriesHow Can I Print a Bash Array with Each Element on a Separate Line?
- May 11, 2025PythonHow Can You Run Python on Linux? A Step-by-Step Guide
- May 11, 2025PythonHow Can You Effectively Stake Python for Your Projects?
- May 11, 2025Hardware Issues And RecommendationsHow Can You Configure an Existing RAID 0 Setup on a New Motherboard?