What Is a Loading Dock and Why Is It Essential for Your Business?
What Is A Loading Dock?
In the bustling world of logistics and transportation, the loading dock stands as a crucial hub where goods transition from one mode of transport to another. Picture a busy warehouse or distribution center: trucks arrive, goods are unloaded, and the rhythm of commerce flows seamlessly. But what exactly is a loading dock, and why is it so vital to the supply chain? This article will delve into the intricacies of loading docks, exploring their design, function, and significance in modern industry.
A loading dock is essentially a platform or area where trucks and other vehicles can load and unload cargo efficiently. It serves as the critical interface between the transportation of goods and their storage or distribution. Typically designed to accommodate various vehicle types, loading docks are equipped with features such as dock levelers, bumpers, and shelters to facilitate safe and effective operations. Understanding the layout and functionality of a loading dock can reveal much about the logistics processes that keep businesses running smoothly.
Moreover, the efficiency of a loading dock can significantly impact a company’s overall productivity and cost-effectiveness. From the design of the space to the technology used in managing shipments, every detail plays a role in optimizing operations. As we explore the various aspects of loading docks, we will uncover how they contribute not only to
Understanding the Structure of a Loading Dock
A loading dock serves as a critical interface between transportation vehicles and storage facilities, allowing for the efficient transfer of goods. The structure typically includes several key components that facilitate loading and unloading processes.
Key elements of a loading dock include:
- Dock Levelers: These devices bridge the gap between the truck and the dock, allowing for smooth transitions when loading or unloading goods. They can be hydraulic, mechanical, or air-powered.
- Dock Shelters and Seals: These are installed around the dock opening to create a weather-tight seal when a truck is backed into the dock. This protects the goods from environmental elements.
- Bumpers: Heavy-duty bumpers are mounted on the dock to absorb impact when trucks are parked, preventing damage to both the vehicle and the dock structure.
- Loading Equipment: Forklifts, pallet jacks, and conveyor belts are commonly used to move goods between trucks and the warehouse.
Loading Dock Design Considerations
The design of a loading dock is crucial for operational efficiency and safety. Several factors must be considered:
- Height and Width: The height of the dock should accommodate the majority of vehicle types that will access it, while the width should allow for easy maneuvering of equipment and personnel.
- Traffic Flow: Adequate space should be planned for the movement of trucks and internal transport vehicles to minimize congestion and enhance safety.
- Safety Features: Incorporating safety measures such as guardrails, anti-slip surfaces, and proper lighting is essential to protect workers and equipment.
Design Element | Consideration |
---|---|
Dock Height | Should accommodate standard truck heights (typically 48-52 inches) |
Dock Width | Minimum of 10-12 feet for safe access |
Traffic Flow | Two-way access for trucks and equipment is ideal |
Safety Features | Guardrails, anti-slip surfaces, and adequate lighting |
Operational Efficiency in Loading Docks
Maximizing the efficiency of a loading dock involves strategic planning and organization. Effective practices include:
- Scheduling Deliveries: Coordinating delivery times can significantly reduce wait times for trucks and streamline operations.
- Training Personnel: Regular training for staff on safety protocols and equipment operation improves safety and productivity.
- Inventory Management: Implementing a robust inventory management system ensures that goods are tracked efficiently, reducing the time spent locating items during loading and unloading.
- Regular Maintenance: Keeping all loading dock equipment in optimal condition minimizes downtime and extends the life of the dock infrastructure.
By addressing these elements, businesses can enhance their loading dock operations, leading to improved logistics and overall supply chain management.
Definition of a Loading Dock
A loading dock is a designated area within a building, typically found in warehouses, distribution centers, and manufacturing facilities, where goods are loaded and unloaded from vehicles. This specialized area is crucial for the efficient management of inventory and logistics operations.
Components of a Loading Dock
The loading dock comprises several essential components that facilitate its operation:
- Dock Levelers: Adjustable platforms that bridge the gap between the dock and the vehicle to ensure safe loading and unloading.
- Dock Shelters and Seals: Structures that protect the loading area from weather elements, improving energy efficiency and worker safety.
- Bumpers: Rubber or metal pads installed on the dock to absorb impact and protect the building and vehicles.
- Safety Barriers: Physical barriers that prevent accidents and ensure safe movement of personnel and equipment.
- Forklifts and Pallet Jacks: Equipment used to move goods onto and off the dock.
Loading Dock Operations
Efficient loading dock operations involve several critical processes:
- Scheduling: Coordination of incoming and outgoing shipments to optimize dock usage.
- Inspection: Checking the condition of goods and verifying shipments before loading or unloading.
- Material Handling: Utilizing equipment like forklifts to move goods safely.
- Inventory Management: Keeping track of stock levels and ensuring timely replenishment.
Types of Loading Docks
Loading docks can be categorized based on their design and operational requirements:
Type | Description |
---|---|
Flush Docks | Aligned with the building wall, providing easy access for loading vehicles. |
Sawtooth Docks | Angled docks allowing multiple vehicles to load simultaneously. |
Enclosed Docks | Fully enclosed areas for temperature-sensitive goods. |
Open Docks | Exposed docks suitable for environments where weather protection is not critical. |
Loading Dock Safety Considerations
Safety is paramount in loading dock operations. Key safety measures include:
- Training: Regular training for personnel on safe loading and unloading practices.
- Personal Protective Equipment (PPE): Use of helmets, gloves, and safety shoes to protect workers.
- Clear Signage: Visible signs indicating pedestrian pathways and vehicle routes.
- Regular Inspections: Routine checks of dock equipment and safety features to prevent accidents.
Technological Advancements in Loading Docks
Modern loading docks are increasingly incorporating technology to enhance efficiency:
- Automated Docking Systems: Equipment that assists in the precise alignment of trucks and trailers.
- RFID and Barcode Scanning: Technologies for tracking inventory and streamlining the loading process.
- Dock Management Software: Tools that manage scheduling, inventory, and logistics in real-time.
Loading Dock Importance
Loading docks play a vital role in supply chain management, impacting overall operational efficiency. Their design, operation, and safety measures are crucial for the seamless flow of goods, directly affecting a company’s productivity and cost-effectiveness.
Understanding the Importance of Loading Docks in Logistics
Emily Carter (Logistics Consultant, Supply Chain Insights). “A loading dock is a critical component in the logistics and supply chain management process. It serves as the interface between transportation vehicles and the warehouse, facilitating the efficient loading and unloading of goods. Properly designed loading docks can significantly enhance operational efficiency and reduce turnaround times.”
James Holloway (Warehouse Operations Manager, Global Freight Solutions). “The design and functionality of a loading dock can greatly impact a company’s productivity. Factors such as dock height, clearance, and equipment accessibility must be considered to ensure safety and efficiency. A well-planned loading dock not only streamlines operations but also minimizes the risk of accidents.”
Linda Tran (Industrial Engineer, Logistics Optimization Group). “Incorporating advanced technology into loading dock operations can lead to significant improvements. Automated loading systems and real-time tracking can enhance inventory management and reduce human error. As e-commerce continues to grow, the role of loading docks will become increasingly vital in meeting consumer demands.”
Frequently Asked Questions (FAQs)
What is a loading dock?
A loading dock is a designated area within a warehouse or distribution center where goods are loaded and unloaded from trucks. It typically features a raised platform that allows for efficient transfer of cargo between vehicles and storage facilities.
What are the different types of loading docks?
There are several types of loading docks, including flush docks, which are level with the warehouse floor; recessed docks, which provide shelter from the elements; and sawtooth docks, designed to accommodate multiple trucks simultaneously. Each type serves specific operational needs.
What equipment is commonly used at loading docks?
Common equipment at loading docks includes dock levelers, forklifts, pallet jacks, dock shelters, and bumpers. These tools facilitate the safe and efficient movement of goods between vehicles and the facility.
What safety measures should be implemented at loading docks?
Safety measures at loading docks should include proper training for personnel, use of personal protective equipment (PPE), installation of safety barriers, regular maintenance of equipment, and clear signage to direct traffic and pedestrian movement.
How do loading docks impact logistics operations?
Loading docks play a crucial role in logistics operations by optimizing the flow of goods, reducing loading and unloading times, and minimizing the risk of damage to products. Efficient loading dock operations contribute to overall supply chain effectiveness.
What are the benefits of having an efficient loading dock design?
An efficient loading dock design enhances productivity, reduces labor costs, improves safety, and minimizes delays in shipping and receiving. It also allows for better space utilization and can improve the overall workflow within a facility.
A loading dock is a crucial component of logistics and supply chain management, serving as the interface between transportation vehicles and storage facilities. It is designed to facilitate the efficient loading and unloading of goods, ensuring that products are moved quickly and safely. The design of a loading dock typically includes features such as dock levelers, bumpers, and safety barriers, all of which contribute to the smooth operation of material handling processes.
One of the primary advantages of a well-designed loading dock is its ability to enhance productivity. By streamlining the loading and unloading processes, businesses can minimize downtime and reduce labor costs. Additionally, a properly managed loading dock can improve safety for workers and reduce the risk of accidents, as it provides a designated area for vehicle and pedestrian traffic to interact safely.
In summary, understanding the significance of a loading dock is essential for businesses involved in shipping and receiving. It not only plays a vital role in operational efficiency but also contributes to overall supply chain effectiveness. Investing in the right loading dock equipment and infrastructure can lead to substantial improvements in both productivity and safety, making it a key area for operational focus in any logistics strategy.
Author Profile
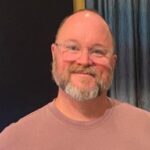
-
I’m Leonard a developer by trade, a problem solver by nature, and the person behind every line and post on Freak Learn.
I didn’t start out in tech with a clear path. Like many self taught developers, I pieced together my skills from late-night sessions, half documented errors, and an internet full of conflicting advice. What stuck with me wasn’t just the code it was how hard it was to find clear, grounded explanations for everyday problems. That’s the gap I set out to close.
Freak Learn is where I unpack the kind of problems most of us Google at 2 a.m. not just the “how,” but the “why.” Whether it's container errors, OS quirks, broken queries, or code that makes no sense until it suddenly does I try to explain it like a real person would, without the jargon or ego.
Latest entries
- May 11, 2025Stack Overflow QueriesHow Can I Print a Bash Array with Each Element on a Separate Line?
- May 11, 2025PythonHow Can You Run Python on Linux? A Step-by-Step Guide
- May 11, 2025PythonHow Can You Effectively Stake Python for Your Projects?
- May 11, 2025Hardware Issues And RecommendationsHow Can You Configure an Existing RAID 0 Setup on a New Motherboard?